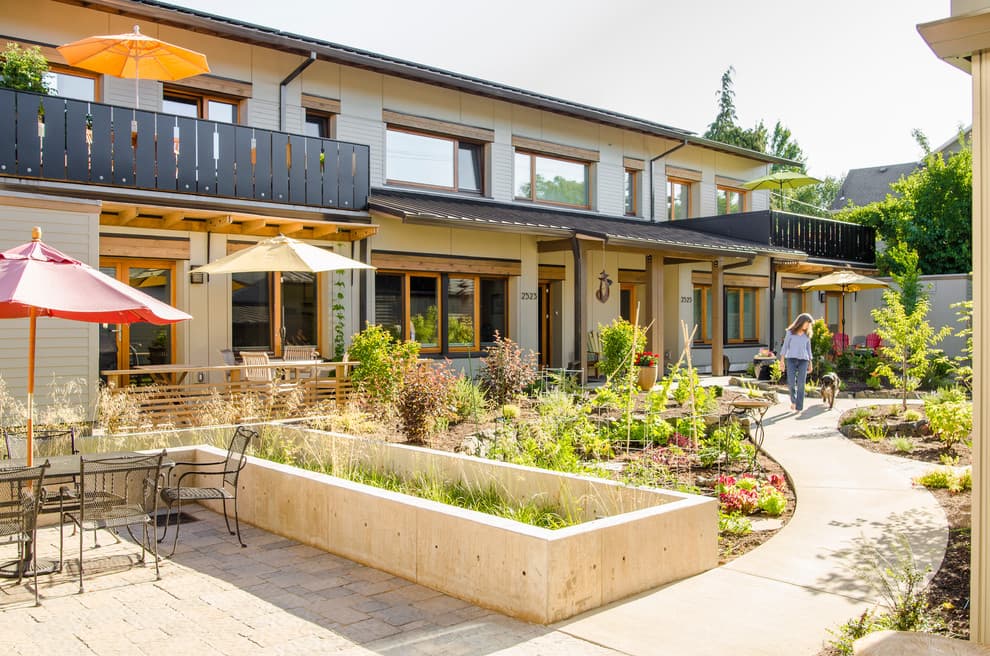
Across the United States, aging baby boomers find themselves living in houses that once accommodated growing families but now feel oversized, difficult to maintain, and environmentally inefficient. Dick and Lavinia Benner, once in this exact situation, now reside in Ankeny Row—a Passive House (PH) cohousing community in Portland, Oregon, featuring five townhouses, one loft apartment, a community hall, and a shared courtyard garden. Their journey from concept to completion involved years of planning, countless meetings, and strategic collaboration.
Finding the Right Location and Partners
Ankeny Row is situated in a historic Portland neighborhood originally developed around streetcar transportation. Though the area experienced decline in the mid-20th century as automobiles became dominant, recent decades have seen revitalization, blending larger residential developments with high-end retail. In 2011, the Benners and another couple discovered the 12,600 ft² (1,170 m²) site that would eventually become Ankeny Row.
The founding residents approached their project methodically:
- Interviewed nine architectural or design/build firms
- Asked three finalists to participate in a design charrette
- Selected Green Hammer Design-Build for their understanding of the project's core objectives and previous Passive House experience
These objectives went beyond typical construction goals, focusing on:
- Minimizing environmental impact
- Creating residences suitable for "aging in place"
- Establishing a social gathering place for a like-minded community
Climate-Responsive Design in Portland's Marine Environment
Portland's climate—wet, mild winters and sunny, mild summers—shares similarities with Central Europe, making the Passive House standard theoretically straightforward to implement. However, differences in construction practices and building product availability created implementation challenges that decreased with Green Hammer's growing experience.
For architects Daryl Rantis and Dylan Lamar, the clients' preference for a central courtyard garden became the organizing principle for the entire site plan:
- Three buildings arranged around a central courtyard
- Strategic building placement to maximize sunlight penetration
- One building with three two-story townhouses along the back
- A second building with two townhouses toward the front
- A third building housing common areas on the main floor with a duplex apartment above
- Living units ranging from 865 to just under 1,500 ft² (80–140 m²)
The "Aha Moment": Achieving Net-Zero with Passive House
A critical insight emerged early in the design process. By prioritizing the Passive House standard and dramatically reducing the community's energy needs, the residents' ambitious net-zero-energy (NZE) goal became achievable with a photovoltaic system covering less than half of the south-facing roof area on the back building. The total PV system capacity is 29 kW.
This elegant solution represents the intersection of Passive House principles with renewable energy generation—using super-efficient building design to make renewable energy systems more practical and cost-effective.
Material Choices: Prioritizing Health and Sustainability
Green Hammer's material palette for Ankeny Row focused on non-toxic, sustainable options:
- Approximately 90% of building components made from wood or cellulose
- Forest Stewardship Council (FSC)-certified lumber and finished wood
- Durable metal roofing
- Limited use of foam products, primarily in foundations
The foundation system demonstrates pragmatic compromise—using an insulated shallow foundation that resembles a styrofoam "bathtub" filled with concrete, with strategic thickness variations at edges, interior footings, and field areas between footings.
Wall Assembly: High-Performance and Vapor-Open
Ankeny Row's wall assembly achieves an impressive R-value of approximately 50 through a thoughtfully engineered system:
- 2 × 6 inches (8 × 24 mm) structural framing (some walls use 2 × 4 framing)
- Structural plywood sheathing exterior to the framing (on the warm side of insulation)
- 9.5-inch (240 mm) wood I-joists furred out from the sheathing
- Dense-pack cellulose insulation filling the I-joist cavities
- Fiberglass mat gypsum sheathing on the exterior
- Diffusion-open membrane with taped seams forming air and weather-resistant barriers
This assembly allows vapor diffusion to both interior and exterior, avoiding moisture accumulation while maintaining exceptional thermal performance.
Air Barrier Continuity and Roof Design
The air barrier system demonstrates meticulous attention to detail:
- Taped membrane wraps continuously from foundation to roof
- Direct connection to the foundation's concrete edge (the air barrier at ground level)
- Monosloped wood trusses (28 inches/700 mm deep) filled with cellulose insulation
- Ventilation channel between trusses and metal roofing creating a vapor-open assembly
Passive Solar Design and Seasonal Comfort
The design takes advantage of solar orientation while preventing overheating:
- Larger windows on south-facing façades maximize winter solar heat gain
- Deep overhangs shade upper-floor south windows in summer
- Awnings protect lower and ground-floor windows
- Careful detailing of projecting elements (awnings, balconies) to minimize thermal bridging
- Strategically placed windows enable stack and cross-ventilation for night cooling
- Ceiling fans in some units enhance comfort with minimal energy use
Mechanical Systems: Minimalist but Effective
Each unit features a carefully selected suite of mechanical systems:
- Individual heat-recovery ventilator providing continuous fresh air
- Mini-split heat pumps for supplementary heating and occasional cooling
- Heat pump water heaters installed in outdoor storage sheds to avoid noise while extracting heat from ambient air
- Top-tier Energy Star-rated appliances
- All-fluorescent or LED lighting
Solar and internal heat gains are expected to provide 67% of annual heating demand, with the mini-splits handling the remainder.
Modeling Challenges and Real-World Energy Use
Using the Passive House Planning Package (PHPP) to simultaneously model three linked buildings presented challenges. Dylan Lamar's experience with Passive House projects in the Pacific Northwest allowed him to select assemblies that would meet annual heating and primary energy demand targets.
However, when sizing the PV system, Lamar had to deviate from PHPP defaults for plug loads and appliances. His observations provide interesting cultural insights:
- Even environmentally conscious American clients typically use more energy than PHPP default assumptions
- European Passive House occupants generally live within PHPP defaults
- For realistic modeling, Lamar incorporates clients' previous utility bills to estimate future non-heating/cooling energy use
Cost Considerations: Experience Reduces Premium
According to Lamar, the cost premium for building to Passive House standards represents a relatively small part of the overall project budget. As Green Hammer has gained experience and developed relationships with subcontractors familiar with Passive House construction methods, other factors—like finish selections and fixture choices—have greater impact on final costs than the high-performance envelope.
Passive House Metrics
The completed project achieved impressive performance numbers:
- Heating energy: 1.37–2.09 kWh/ft²/year (14.76–22.46 kWh/m²/a)
- Cooling energy: 0.07–0.21 kWh/ft²/year (0.73–2.27 kWh/m²/a)
- Total source energy: 12.07–14.83 kWh/ft²/year (130–160 kWh/m²/a)
- Treated floor area: 1,312–3,965 ft² (122–368 m²)
- Air leakage: 0.5–1.0 ACH50
Ankeny Row demonstrates that Passive House principles can effectively address multiple needs simultaneously—providing comfortable, energy-efficient homes where residents can age in place while fostering community connections and minimizing environmental impact. As more baby boomers seek sustainable downsizing options, this Portland project offers valuable lessons in combining technical performance with social goals.
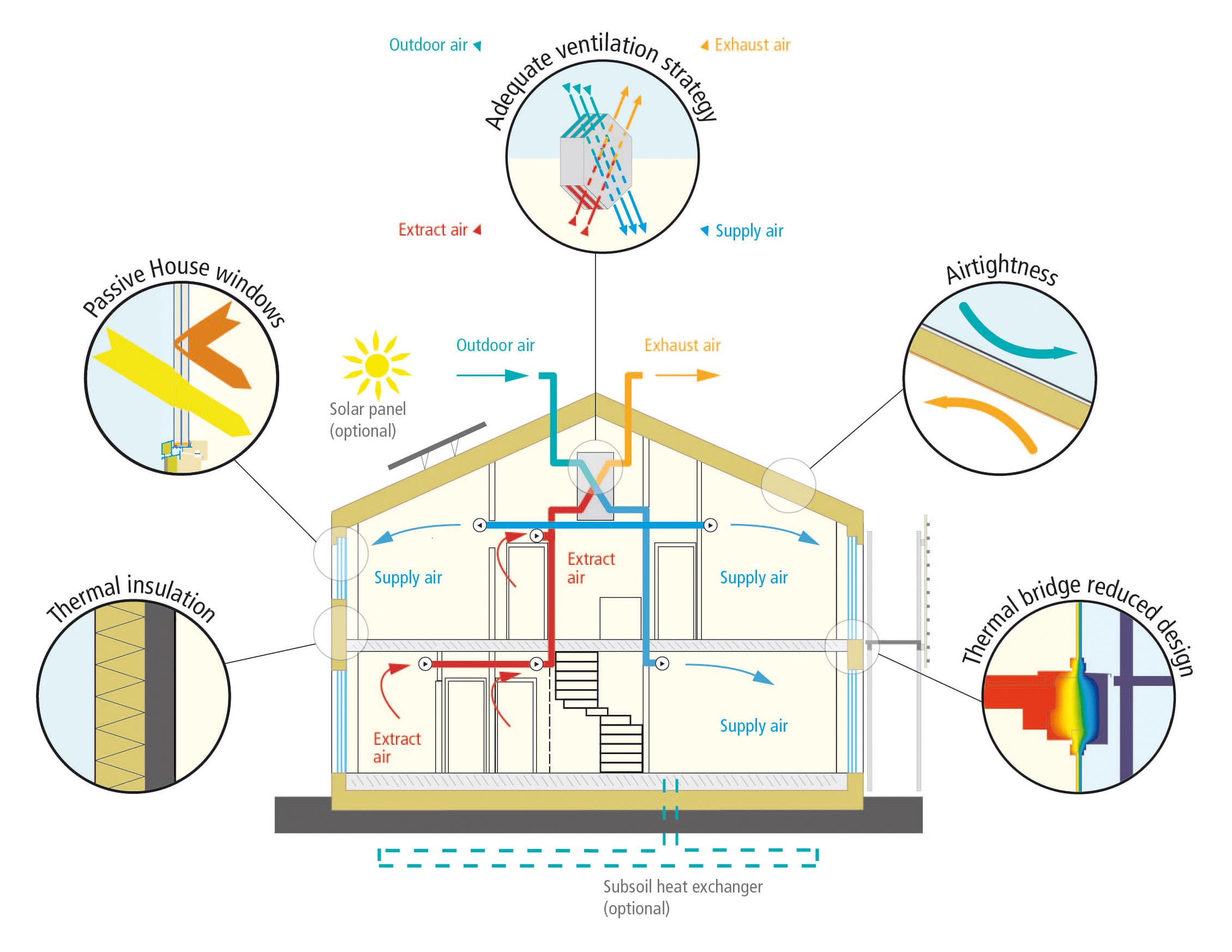
Evolving Passive House Standards: Adapting to Climate and Context
Explore the evolution of Passive House standards from the original 'Classic' model to climate-specific certifications like PHIUS and EnerPHit, reflecting a growing need for flexibility and global applicability.
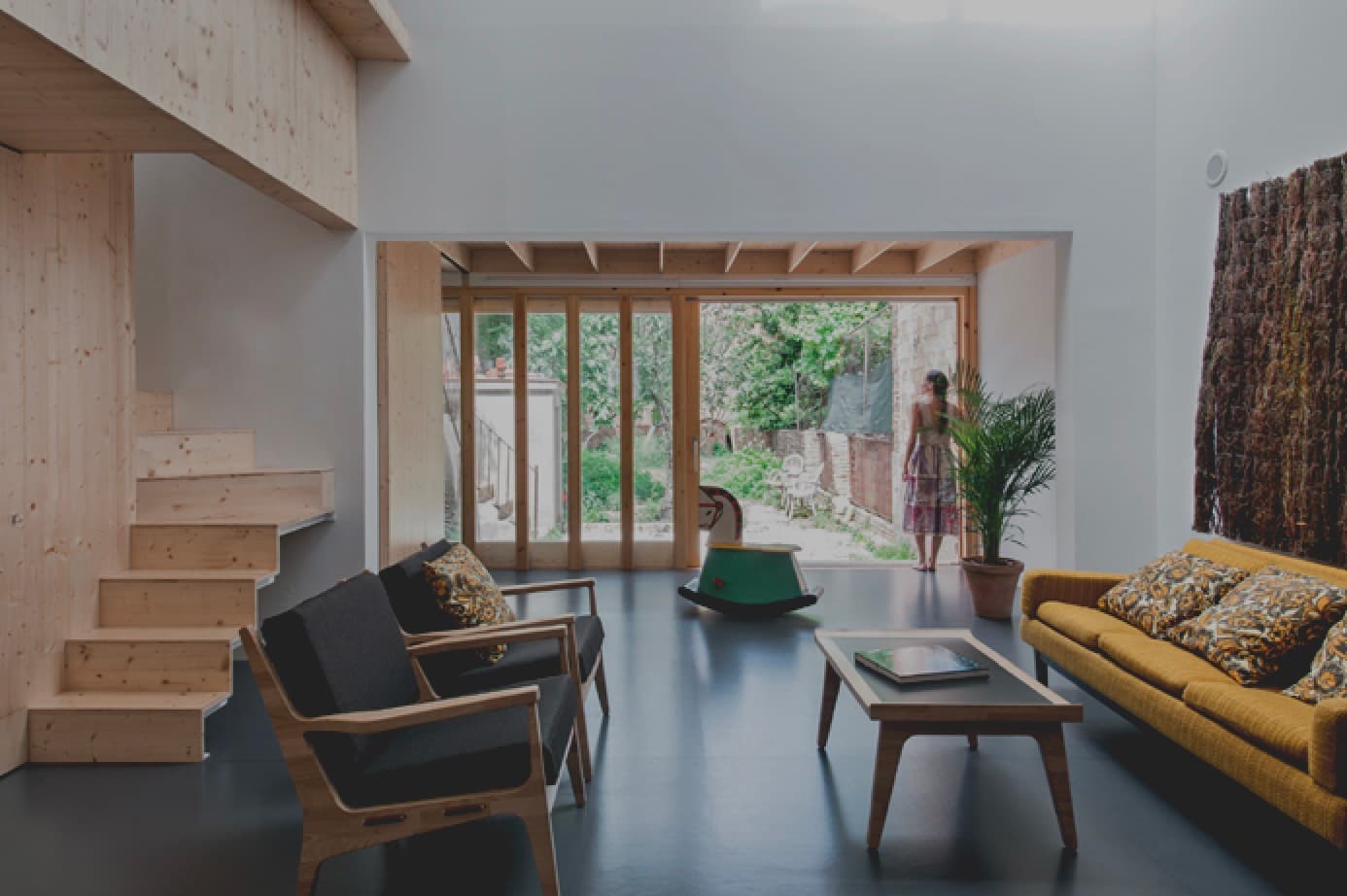
Applying Passive House Principles in Different Climates
Discover how Passive House principles can be successfully adapted to diverse climates worldwide, with real-world examples and practical solutions for maintaining comfort and efficiency in any environment.
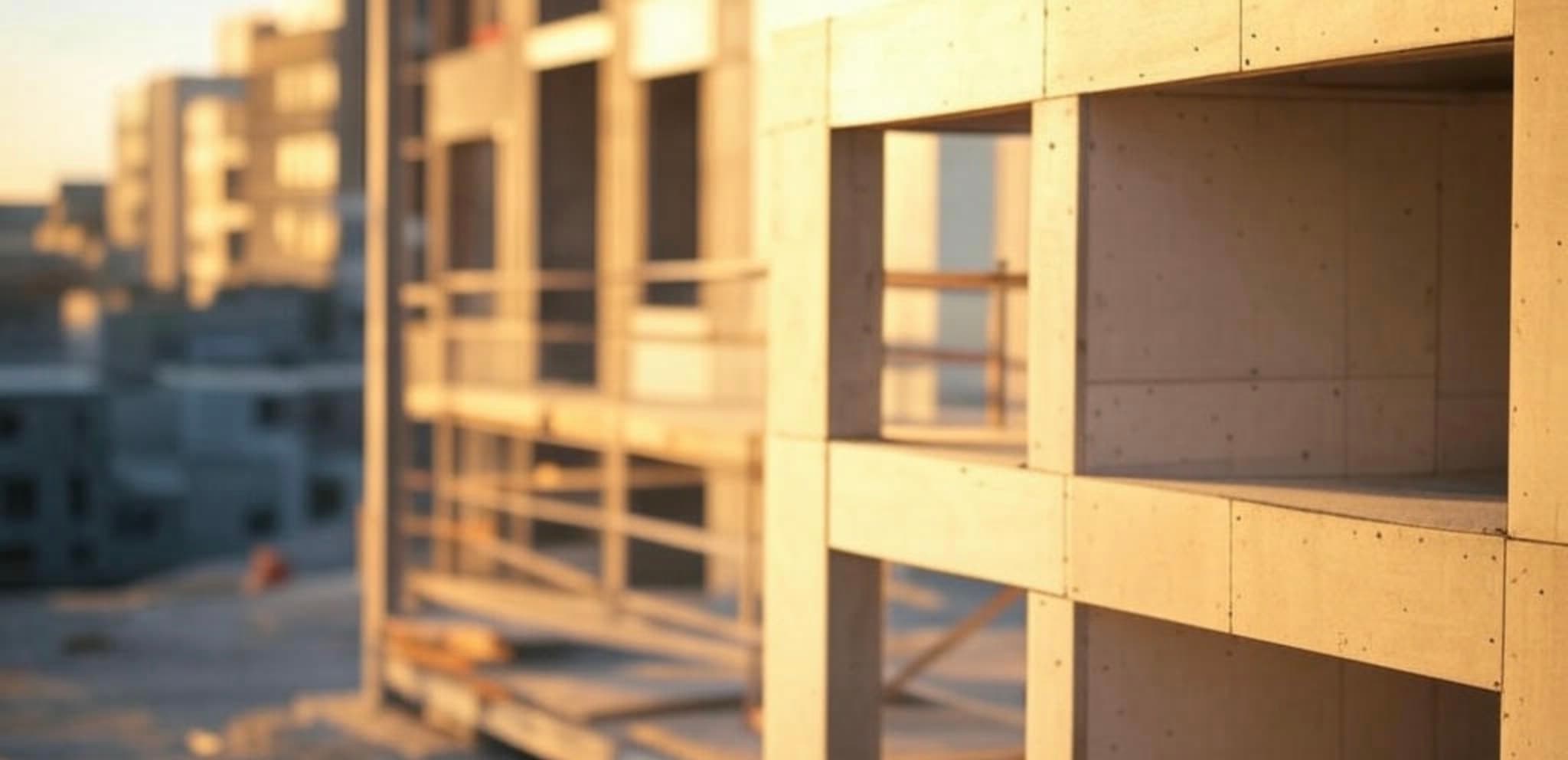
Seven Principles of Passive House Design: Building for Efficiency and Comfort
Explore the seven foundational principles of Passive House design that ensure superior energy efficiency, exceptional indoor air quality, and lasting comfort in every climate.